色〜んな目で 世間の出来事をチェック!
ウの目・ネコの目・トンボの目
『はやぶさ2プロジェクト』の成功を支えた“ニッポンの中小企業のとんがった技術”。ニッチでも超繊細なワザと、飽くなき情熱が拓いた深宇宙探査の道!!
カプセル内に5.4グラムのリュウグウのサンプル! 太陽系の起源と生命の原材料の解明に町工場の技術が生き!
6年間、往復52億キロの大航海を終え、「小惑星リュウグウの砂・粒」が大量に入ったカプセルを地球に持ち帰った『はやぶさ2プロジェクト』。そこには、「ニッポンの中小企業の“とんがった技術”が成功を支えた」という事実が何度も紹介されていますが、一体どのような技術で貢献したのかを見てみましょう。
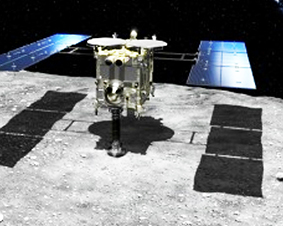
もちろん『はやぶさ2プロジェクト』には宇宙関連やロケット開発の大手企業・上場企業が数多く参画しているのですが、その中に混じって、町工場の“職人技”とも言えるようなニッチな超専門的な技術や、職人さんたちの飽くなき情熱を見ることができます。
ここでは、その中小企業・零細企業の人たちの「支え」の一端を紹介していきたい、と思います(これらは、ごく一部であることをご容赦ください。また参考資料などを使わせていただいたメディア、機関の皆様に御礼を謹んでお礼を申し上げます)
異常な高温と衝撃に耐えるレベルへの到達へ
数えきれない実験を繰り返す
有限会社・清水機械は、東京都江東区にある従業員5人の町工場です。その5人はすべて現場に出る職人さんたちですから、ホームページもありません。いや、ホームページなどなくても、「清水機械さんにしかできないから、頼んでみよう!」という依頼が来るのです。
清水機械が得意とするのは「いろいろな機械・装置の試作品の製造」という分野。
産業用機械の中でも、ロケットに積む込む装置や機械部品は、発射され、小惑星に着陸し、無事帰還するためには、途中、何度も高熱にさらされたり、惑星に衝突したりするため、「非常に高度な精密さと強度・軽さ」という矛盾した課題を克服しなければならないのです。
そのカベを越えるためには「まず、部品の試作品を作って、何度の実験を繰り返す」しかありません。
とくに、「ターゲットマーカー」という装置は、小惑星に投下され、着地点を示す灯台のような装置です。無重力状態でも正確に作動し、軽くても落下の衝撃に耐えなければなりません。
アルミ板を「深絞り」という人による技術で非常に薄い半球状に加工し、球殻状にした薄い板を組み合わせてテープで接着し、「試験用のターゲットマーカーの外郭を作る工程」が欠かせないのです。そこで、清水機械の出番が来たのです。
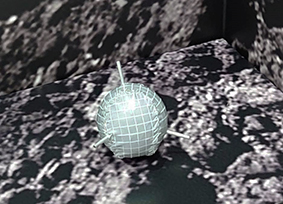
「はやぶさ2に搭載されたターゲットマーカー」
(資料:JAXA)
清水機械は、この難テーマ受け持ったのです。
社長の山崎秀雄さんは、新潟県南魚沼市に生まれ、東京タワーが完成した1958年に“就職列車”で上京し、はじめは新宿の菓子店に就職。2年後に清水機械の前身の町工場に就職した人です。
「例えば、大気圏出るときの摩擦熱の実験用の模型作り。何1000度の温度をかけると10秒くらいで溶けてしまのです。本当は80秒くらい持たせたい。そういう実験を何度も何度も繰り返しやるので部品も相当な数を作らなければならないのですよ」と話しています。
数えきれないほど模型を作って、実験を何度も何度も繰り返し、はじめて宇宙の旅に耐えうる製品にたどり着いたのです。
「ウチだけのノウハウや技術じゃ解決できない部分も多いですよ。小さいところがいっぱい集まってスクラム組んでね、大きいメーカーさんに負けないようにしているんです」
町工場の執念が、この大プロジェクトの根底を支えたと言えるでしょう。
(資料参考:下町探偵団 :www. shitamachi.net
NEC:宇宙開発利用への取り組み「宙への挑戦」
「人の手」で丁寧に畳み込むことで
“最後の一瞬”にきれいに開いたパラシュート
「はやぶさ2」は「りゅうぐう」で採取した砂粒が入ったカプセルをオーストラリアの地に投下しました。「軟着陸して成功するか」、「地表に激突して失敗するか」という、その“着地の一瞬”が、このプロジェクトの成果を大きく左右しました。
今回のカプセルの「安全な着地」に大きな役割を果たしたのが「パラシュート」です。
パラシュート作成を担当したのは、福島県田村市にある藤倉航装株式会社の船曳工場です。
藤倉航装はすでに歴史も80年以上、資本金は5000万円ですから、中小企業とは言えない規模です。落下傘、救命胴衣などの製造では、他に類を見ない専門技術を有しています。
今回、「はやぶさ2」のカプセルに搭載されたパラシュートは、大きさは直径2メートル、重さは約700グラム。レーダーで検知しやすくする布が取り付けられました。
生地には真空空間に強いポリエステルを採用し、工場スタッフがミシンで手縫いしているのです。さまざまな形状の繊維品を縫い合わせるため「機械では、細かい部分の作業ができず、人の手の繊細な感覚が必要だったから」なのです。
NHKテレビのニュースなどにも映し出されましたが、パラシュートの生地の一部をあえて破いて試したり、つないであるヒモを何本か切って試したり、起こりうる“不測の事態”を何度も繰り返し、着陸の実験を行っています。
「これこそ“エビデンス”をしっかりと集めて、成功への道筋を見つけ出した」と言えるでしょう。
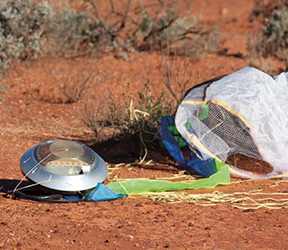
オーストラリアの地にカプセルの着地成功を導いたパラシュート (JAXA資料)
とりわけ、パラシュートは狭い空間に6年間という長期間閉じ込められ、必要な最後の瞬間にパッと開かなければならないのですが、普通であれば、機械で精緻に折り畳むのが最良と思われがちです。
しかし、実際には「“人の手の柔軟さ”によって、丁寧に折り畳んで積み込んでいったほうが、最後の瞬間にパラシュートがきれいに、問題なく開く」というポイントにたどり着いたのです。
6年間にわたる「はやぶさ2」の長旅。その最後の一瞬を担ったニッポンの技術力の高さと情熱を、そこに見ることができるのです。
ちなみに、この藤倉航装では、「コラボ商品シリーズ」として、薄く軽量なパラシュート素材を使った、リュックサックやトートバッグも一般向けに製造・販売しているのです。職人によりボンディング加工された商品だそうです。
・藤倉航装ホームページ :http://www.fujikura-parachute.co.jp/
<藤倉航装コラボシリーズ | 職人が生み出す、こだわりのメンズバッグ・カバン通販>ttps://www.seal-store.net/?mode=grp&gid=1345081
(資料:NHKニュースなど)
「できないとは言わない会社」が実現させた
不純物ゼロに磨き上げた素材
「小惑星りゅうぐう」の砂や石粒を地球に持ち帰るためには、その格納容器が、不純物が絶対に入り込まないほど精密に磨き上げられていなければなりません。
格納装置内部の精密研磨を担当したのは宮城県宮城郡利府町の株式会社ティ・ディ・シーという会社です。
その超精密なナノレベルの研磨技術は、世界トップクラスと言われ、「できないとは言わない」という言葉を会社の理念に掲げているのです。
前回の「はやぶさ1プロジェクト」で回収した小惑星物質は最大サイズ70ミクロン、最小サイズ20ミクロンの小さなものだったそうです。そのため容器の切削面が粗いと貴重な研究サンプルにダメージが入ってしまいます。
「りゅうぐう」の砂を無事に持ち帰るためには、運搬中にこすれて容器の成分が混入したりするのを防ぐため、アルミ製容器の内側表面の凹凸が100万分の1ミリ以下という高い精度で磨き上げる必要があったのです。内面をピッカピカの鏡面に限界まで磨いたそうです。
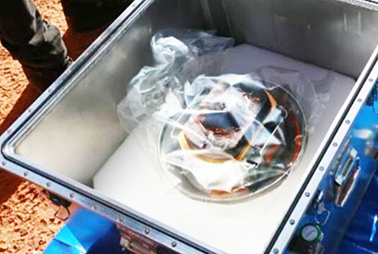
不純物ナシのカプセル容器が「りゅうぐうの砂石」を持ち帰ってきた(JAXA)
ライブ配信で帰還を見届けたという赤羽優子社長は「(着陸の成功を見届け)感動で泣きそうになった」と話します。「重要なミッションに関わることができてうれしい限りです。中身や容器がどうなっているのか知るのが楽しみで、また次へつなげていけます」と語っています。
(参考資料:ダイヤモンド・オンラインなど)
着地点を照らし出したランプ
長年のロケットとの関わりを受け継いだ職人のワザ
「はやぶさ2」プロジェクトで、小惑星「りゅうぐう」の岩石を採取するというシーンは、このプロジェクトの最大の見せ場だった、と言ってもいいかもしれません。
小惑星に向けて投下された「(前述の)ターゲットマーカー」と呼ばれるボールが暗闇の宇宙空間の中で目指すのは、「フラッシュランプ」で照射され、示された着地点です。
このフラッシュランプの開発を担当したのが、神奈川県海老名市にあるミヤタエレバム株式会社という会社です。
従業員は40名ほどですが、硬質・石英ガラス加工の専門メーカーで、カメラや医療機器などに使うランプを製造している会社です。
このミヤタエレバムが手掛ける製品は、機械での製造が難しいものが多く、「熟練の職人が手作業で生み出さざるを得ない」と言います。
小惑星「イトカワ」で微粒子を採取し、2010年に地球に帰還した初代「はやぶさ」でも同社が開発した技術が採用されています。
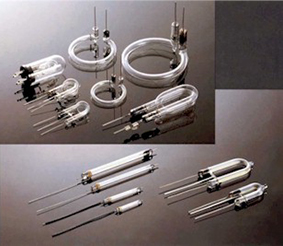
ミヤタエレバムの技術力の高さを証明する「フラッシュランプ」製品群
はやぶさ2に搭載されたフラッシュランプは、実は、一般的なカメラのフラッシュのように、キセノンガスを封入したガラス管の両端に高い電圧をかけて発光させていますが、漏電を防ぐ効果を狙ってガラス管の両端を刀のつばのような形にしています。
職人のワザを長年にわたって引き継いでいるミヤタエレバムでしかできない、繊細な加工が施されているのです。
「宇宙空間では何が起こるかわかりません。宇宙での故障やその時のリスク回避など、3年もの試行錯誤を重ねながら完成させたのが今回のフラッシュランプです」。
ミヤタエレバム ホームページ: www.elevam.com
(参考資料:「タウンニュース」社など)
独自の技術をさらに磨き上げ、検証を重ね
たどり着いた結果が「はやぶさ2」の成功を支えた
このほかにも、「はやぶさ2プロジェクト」には、私たちが考えている以上に、中小企業のモノづくりの技術が生きている。そのどれもが、世界トップレベルの精度をもち、職人芸ともいえる“人のワザ”によって生み出されたものだったのです。
ここで、その一端の挙げてみましょう。
●株式会社キットセイコー(埼玉県羽生市)
チタン合金やステンレスなどの精密切削によって特殊なネジや微細な航空機用部品などを作るのが得意な会社です。従業員は23名ほど。
今回の「はやぶさ2」では 本体に取り付ける機器を留める「六角穴付きボルト」と呼ぶキットセイコー製の特殊ねじが約500本が使われていました。
直径3~6ミリを中心に長さは数センチから30センチまでのものなどさまざまだが、 特徴的なのは“64チタン合金”と呼ばれるその材質。インプラント(人工歯根)などに試使用されるチタン合金の延長線で、ゴルフクラブで使われている純チタンよりも硬く、軽くて壊れにくいといいます。
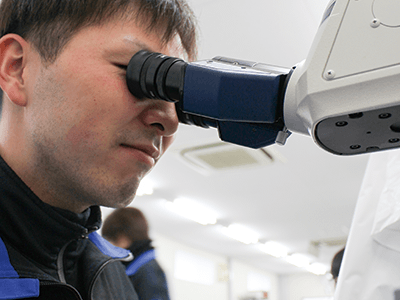
精密なねじづくりは、これまでも多くの宇宙探査の成功を導いてきた。(キットセイコー)
ねじの製造はほぼすべてが手作業で、手書きの図面を見ながら、長さ3メートルほどの棒状の材料を必要な分だけ、精緻に切断したり、削ったりしながら形を整えていって完成させたものでした。
キットセイコー ホームページ:www.kitseiko.co.jp
(参考資料:「ITメディアニュース」)
●タマテック株式会社(福島県鏡石町)
「はやぶさ2」では、地下物質の採取をするためにりゅうぐうにクレーターを作るシーンが話題になりました。金属弾を惑星の地表に打ち込むためには「衝突装置」がカギを握るのですが、その衝突装置の中に、爆弾を詰める金属容器を製造したのがタマテックという会社です。
とにかく厳しい重量制限が課せられているため、当初は軽いアルミを使った装置で実験していたのですが、真空環境では不具合が生じることがわかり、素材を思い切ってステンレスに変更。経験のない厚さ1ミリの容器作りに挑んだことが成功に結び付いたのです。
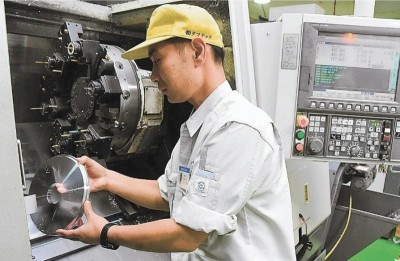
職人のワザが精密なボルトを生み出していくJAXA資料)
・タマテック ホームページ:https://www.tamatec.net/
(参考資料:「福島民報」」)
●株式会社 下平製作所(横浜市金沢区)
今回、「はやぶさ2」では、りゅうぐうの砂・石を試料として無事、採取できたのですが、その際に大きな役割を果たしたのが「サンプラーホーン」という試料採取装置です。
このサンプラーホーンの精度を決めるのが、そのキーとなるバネ部品で、制作したのは横浜市の下平製作所という会社です。
従業員は30名ほどで航空機や人工衛星の部品を製造しており、宇宙との関わりは長いのです。
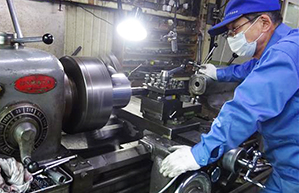
手作りで挑んだ精密ねじの製作には、長い歴史の積み重ねと職人の技が込められている。
下平製作所が作った、採取装置のバネを結合させる部品などは、それぞれ100分の1ミリ単位で要求される製品がほとんど。要求された精度で800個以上も製作し、納入しなければならなかったのです。機械で作成できれば簡単なのかもしれませんが、なにしろ「手作り」です。
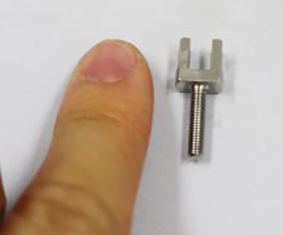
「はやぶさ2」のサンプラーホーン結合に使われた精密ねじ
(資料:慶応熟生新聞)
下平製作所の川口社長は。「宇宙空間では100分の1ミリのズレが重なると大きなズレになって、トラブルの原因になってしまいます。最後は機械ではなく、人間の五感で仕上げています。重要なのは、最終調整は機械任せにしないことなんですよ」と話しています。
下平製作所 ホームページ:shimohira-ss.co.jp
(参考資料 :「iza」
「慶応塾生新聞」
●東成エレクトロビーム・東成イービー東北株式会社(東京都西多摩郡瑞穂町)
圏央道の青梅ICに近い瑞穂町に立地する東成エレクトロビームは、独自に開発した “電子ビーム” により、従来不可能だった異種金属同士の接合を実現させ、小惑星探査機「はやぶさ2」に採用されるなど、航空宇宙産業を支えています。
「はやぶさ2」の目的地となった小惑星「リュウグウ」では、爆薬を使って小惑星表面を掘り返し、内部の標本を持ち帰ろうという意欲的なミッションに挑戦しました。そのカギをを握ったのが「インパクター(衝突装置)」と呼ばれる装置で、爆薬に点火し、表面を覆う銅板を飛ばし、それを砲弾のように打ち込んで小惑星表面に“人工クレーター”を作ろうという人類初の挑戦だったのです。
そのインパクターの核心部分が、爆薬を収めるケースの、銅とステンレスの異種金属接合部。それを独自技術の「電子ビーム溶接」で行ったのが、この技術で高いノウハウを有する東成エレクトロビーム株式会社(東京都西多摩郡瑞穂町)の子会社で、福島県郡山市に拠点を置く東成イービー東北株式会社なのです。
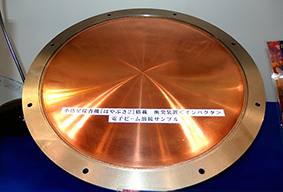
「インパクター」の試作品。円形の銅板と、ケースのステンレスを、周長約1mにわたって電子ビームで溶接している。
インパクターが狙った位置に飛ぶということは、先端にある銅とステンレスの皿状の構造物が均一に溶接されている必要があり、同時に、爆圧時には均等に剥離する必要があります。
「溶接は取れてはいけない、でも必要な時には取れる」
この衝突装置は電子ビーム溶接機により溶接された物です。
この相反する要求、これを銅とステンレスという、熱伝導率や融点の異なる異種金属で行うには長年の経験に裏付けられた高度な技術力が求められます。それを、検証に検証を重ねて、実現させたのが同社の電子ビーム溶接だったのです。
・東成エレクトロビーム株式会社 :http://www.tosei.co.jp
・東成イービー東北株式会社 :http://ebtohoku.co.jp
(参考資料「溶接ニュース」より)
●株式会社松田技術研究所(東京都板橋区)
独自の防振技術を持つ会雄社で、「防振サス」「防振キャスター」などを開発しています。
従業員はわずか10名ほどですが、 世界初となる高い衝撃吸収率を実現して、98.5%もの振動を吸収する技術を有しているのです。
宇宙航空研究開発機構(JAXA)宇宙科学研究本部・月惑星探査プログラムグループが、この松田技研の「防振技術の高さ」を知り、地球に戻ってくる「カプセル」を安全に輸送するための「回収ボックス」に、この防振技術を採用したのです。
先行試作段階では、輸送中の振動を1.5G以下にすることが求められ、オーストラリアの大陸を車(ジープ)で運び、飛行機で日本まで輸送できること、というのが大きな課題でした。松田技研では、ゼロからの仕様を考え、何度も振動データを計測し、設計変更を重ね、改良を繰り返し、安全輸送を実現できる「回収ボックス」をJAXAに納めることができたのです。
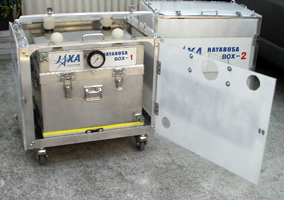
カプセルを安全に運ぶために、極力、振動を抑えた「回収ボックス」(JAXA)
松田技研の松田真次社長は、子どものころから根っからの“機械好き”で、中学生のときの夢は電車の運転士。新幹線構想の発表を見て発奮し、昭和鉄道高校への入学を果たし、その後はヤマト運輸、ホンダといった大企業にも勤めています。「商品の寿命は短く、すぐあきられる。もっと寿命が長く、社会に貢献できるものがやりたかった」という思いを持っていたのです。宇宙関連で培った技術を活かして、これまで免振機能を備えた「車いす」や、移植手術に使う臓器運搬用の容器なども制作しています。
松田技術研究所 ホームページ:www.mrd-matsuda.co.jp
中堅・中小企業の独自技術が集結して
「はやぶさ2」プロジェクトの成功が生まれた!
この他にも、「はやぶさ2プロジェクト」で、大きな役割を果たした中小企業は数多くあります。
ロケットブースターの切り離し部や、太陽電池パドル駆動部、探査ロボットの脱着部など、各種の駆動箇所の潤滑油を開発した 川邑研究所(東京目黒区)。
イオンエンジンに採用され、宇宙空間の長旅を支えたサマリウムコバルト磁石を使った磁気回路を開発したトーキン(宮城県白石市)。
宇宙空間にある「りゅうぐう」は、直接太陽の光にさらされている部分の温度は100度以上にもなり、逆に、日陰の部分はにマイナス100度以下にもなるという過酷な条件にさらされています。その熱を防ぐための多層断熱材「サーマルブランケット」を開発したクロスメディア(相模原市緑区)。
「はやぶさ2」をりゅうぐうへ導き、地球へ帰還させる原動力イオンエンジンの推進剤となる「キセノンガス」の供給を担ったのが、産業用ガスの専門商社ウエキコーポレーション(東京都大田区)
など、その他にも多くの中堅・中小企業の専門的な技術、ノウハウが生きて、「はやぶさ2」の成功が実現したのです。
宇宙にはまだまだ解明されていない謎の部分が多く存在しています。そこを突き付けていくと、「人類誕生」の秘密にもたどり着くことができるかもしれないのです。
「はやぶさ2」は、カプセルを地球に投下したあとも、また、新たな旅を続けています。日本の中小企業がそれぞれ追い求めている精度、新たな技術・手法にもまだまだゴールは見えていないのかもしれません。挑戦は続くのです。
参考: JAXA(宇宙航空研究開発機構):https://www.jaxa.jp